|
|
Online shop |
 |
Static mixing systems provide a significant improvement in the efficiency of pump mixing processes. Much shorter mixing time and lower energy consumption can be expected.
Example of typical biodiesel process application: feeding the alcohol / hydroxide mixture into the vegetable oil stream as it is recirculated through the pipe mixer.
|
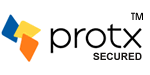 |
 |
 |
 |
   |
 |
 |
|
   |
 |
|
|
|
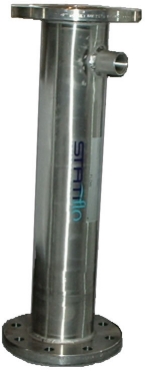 |
|
|
|
|
|
Inside the pipe, there are three elements that split the stream of liquid and create vortices and shearing effects. The elements are arranged, so that the centre element generates a vortex in the opposite direction to the other two. This clockwise / anticlockwise motion ensures the liquid mixture leaving the pipe is homogeneous. |
|
|
Key benefits |
- Highly efficient mixing
- Low energy consumption (pressure drop)
- No moving parts - maintenance free operation
- Ease of installation
- Minimal space requirement
- Totally enclosed pipe design
- Available in a range of sizes
|
|
|
|
|
|
|
Construction |
- 316 Ti stainless steel
- Conforms to DIN 5009.3.1 - B
- 100°C design temperature
- 10 barg design pressure
|
|
|
|
|
Sizes |
Diameter |
Elements |
Length |
Dosing boss |
Weight |
(mm) |
|
(mm) |
|
(kg) |
100 |
3 |
615 |
25mm NB female |
14 |
80 |
3 |
500 |
25mm NB female |
11 |
50 |
3 |
445 |
25mm NB female |
7 |
50 |
4 |
520 |
25mm NB female |
7.5 |
25 |
3 |
210 |
25mm NB female |
2.7 |
25 |
4 |
248 |
25mm NB female |
2.9 |
|
|
|
|
|
|
|
|
|
|